Deterioration of Concrete and Remedial Measures
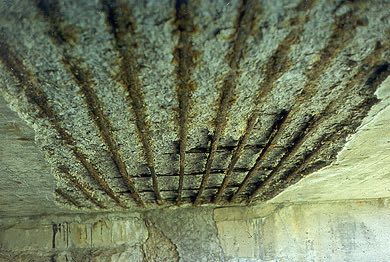
Deterioration of concrete refers to the process of degradation or damage that occurs in concrete structures over time due to various factors. Several common causes of concrete deterioration include:
Chemical Attack:
Exposure to aggressive chemicals, such as acids, sulfates, chlorides, and alkalis, can lead to chemical reactions that weaken the concrete and cause deterioration.
Corrosion of Reinforcement:
When steel reinforcement within the concrete is exposed to moisture and oxygen, it can corrode, leading to cracking, spalling, and reduced structural integrity.
Freeze-Thaw Damage:
Repeated cycles of freezing and thawing can cause the water within the concrete to expand and contract, resulting in internal pressure and cracking.
Alkali-Silica Reaction (ASR):
ASR occurs when reactive silica present in certain aggregates reacts with the alkaline cement paste, causing expansion and cracking over time.
Erosion and Abrasion:
Physical wear and tear caused by abrasive materials, water flow, wind, or impact can result in surface deterioration.
Decomposition of Concrete Depends on:
- Porosity of concrete
- The concentration of the acid
- Solubility of the Acid Calcium Salt
- Fluid Transport through the concrete, its temperature, and pressure
Remedial Measures:
To address concrete deterioration, several remedial measures can be taken, depending on the specific cause and extent of the damage. Here are some common approaches:
Repair and Patching:
Damaged concrete can be repaired by removing the deteriorated portion and replacing it with fresh concrete or using specialized repair materials. This helps restore structural integrity and prevent further deterioration.
Protective Coatings:
Applying protective coatings, such as epoxy coatings or sealants, can provide a barrier against chemical attack, moisture penetration, and abrasion. Coatings should be chosen based on the specific exposure conditions and compatibility with the substrate.
Corrosion Control:
To mitigate reinforcement corrosion, techniques like cathodic protection, corrosion inhibitors, and protective coatings for reinforcing steel can be employed to prevent or slow down the corrosion process.
Water Drainage and Waterproofing:
Proper drainage systems and waterproofing measures, such as installing effective membranes, can help prevent water ingress, minimizing the potential for freeze-thaw damage and chemical attack.
Alkali-Silica Reaction Mitigation:
Mitigating ASR involves using low-alkali cement, selecting non-reactive aggregates, or employing chemical admixtures to reduce the potential for expansion and cracking.
Regular Maintenance and Inspection:
Implementing a comprehensive maintenance program that includes regular inspections, cleaning, and repairs can help identify and address deterioration at an early stage, preventing further damage.
- Calcium silicates can be used to fill the pores and decrease the permeability. This can be done by treating calcium hydroxide with diluted sodium silicate (also known as Water-Glass)
- Pores can also be filled by treating Calcium Hydroxide with Magnesium Fluosilicate followed by the formation of Colloidal Silicofluoric Gel to withstand acid attack
- Allowing the concrete to dry before exposure causes the formation of a calcium carbonate film produced by the action of CO2 on lime. This film blocks the pores and reduces the permeability of the surface layer. Thus precast concrete is appreciated.
- The above method is not a permanent solution. For more protection, the concrete is subjected in a vacuum to silicon tetrafluoride gas which reacts with the lime as follows.
2Ca (OH)2 + SiF4 ------> 2CaF2 + Si (OH)4
This treatment can only be applied to precast concrete, which is then known as Ocrat-Concrete.
It's worth noting that the selection of appropriate remedial measures should be based on a thorough assessment of the specific deterioration mechanisms affecting the concrete structure. Consulting with a qualified structural engineer or concrete specialist is recommended to determine the most effective and suitable remediation strategies.
Surface Treatments for Concrete
Surface treatments are protective coatings or applications that are applied to the surface of the concrete to enhance its durability, appearance, and resistance to various forms of deterioration. These treatments are typically applied to existing concrete surfaces and can help extend the service life of the structure. Here are some common types of surface treatments:
Sealers:
Sealers are thin coatings that are applied to the concrete surface to provide protection against moisture penetration, staining, and chemical attack. They form a barrier that reduces the absorption of water and other contaminants, helping to preserve the concrete's integrity. Sealers can be clear or pigmented and are available in different formulations such as acrylic, epoxy, polyurethane, or silane/siloxane-based sealers.
Epoxy Coatings:
Epoxy coatings consist of two components that are mixed together and applied to the concrete surface. They form a durable, high-strength coating that offers excellent chemical resistance, abrasion resistance, and protection against impact or heavy loads. Epoxy coatings are commonly used in industrial or commercial settings where a high-performance protective layer is required.
Polyurethane Coatings:
Polyurethane coatings are similar to epoxy coatings in terms of their protective properties but offer enhanced UV resistance and flexibility. They are often used in outdoor environments or areas exposed to sunlight, as they can withstand prolonged exposure without yellowing or degrading.
Stains:
Concrete stains are used to enhance the aesthetic appeal of concrete surfaces by adding color or creating decorative patterns. Stains can be either acid-based or water-based, and they penetrate into the concrete to produce a permanent coloration. They are commonly used in interior spaces, such as floors or countertops, as well as exterior applications like patios or driveways.
Anti-Graffiti Coatings:
Anti-graffiti coatings are specialized coatings applied to concrete surfaces to make it easier to remove graffiti or prevent its adhesion. These coatings create a protective layer that allows graffiti to be easily cleaned off without damaging the underlying surface.
Concrete Overlays:
Concrete overlays involve the application of a thin layer of new concrete material over the existing concrete surface. Overlays can be used to repair surface defects, improve appearance, or add a decorative finish. They can be integrally colored, stamped, or stained to achieve the desired aesthetic effect.
Surface Hardeners:
Surface hardeners are chemical treatments that penetrate into the concrete surface to chemically react and densify the top layer. This process enhances the abrasion resistance and durability of the concrete, making it more resistant to wear, dusting, and surface deterioration.
When selecting a surface treatment, it's essential to consider factors such as the specific requirements of the application, environmental conditions, desired appearance, and the type and condition of the existing concrete. Consulting with a professional concrete contractor or surface treatment specialist is advisable to determine the most suitable treatment for your specific needs.