Materials Used in Bridges Construction
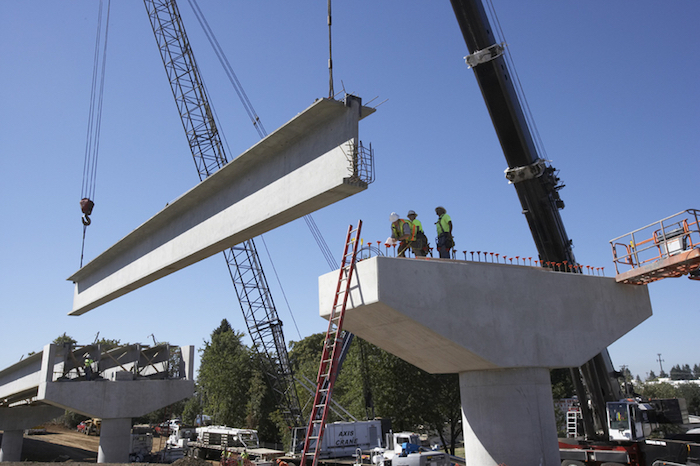
Watch Bridge Engineering Tutorial Videos
Bridge Construction Materials:
The traditional building materials for bridges are stones, timber and steel, and more recently reinforced and pre-stressed concrete. For special elements aluminum and its alloys and some types of plastics are used. These materials have different qualities of strength, workability, durability and resistance against corrosion. They differ also in their structure, texture and color or in the possibilities of surface treatment with differing texture and color. For bridges one should use that material which results in the best bridge regarding shape, technical quality, economics and compatibility with the environment.
1. Stone:
The great old bridges of the Etruscans, the Romans, the Fratres Pontifices of the middle ages (since about 1100) and of later master builders were built with stone masonry. The arches and piers have lasted for thousands of years when hard stone was used and the foundations constructed on firm ground. With stone one can build bridges which are both beautiful, durable and of large span (up to 150 m).
Unfortunately, stone bridges have become very expensive. Over a long period, however, stone bridges, which are well designed and well built, might perhaps turn out be the cheapest, because they are long-lasting and need almost no maintenance over centuries unless attacked by extreme air pollution.
Stone is nowadays usually confined to the surfaces, the stones being preset or fixed as facing for abutments, piers or arches. Of course, sound weather-resisting stone must be chosen, and fundamental rock like granite, gneiss, porphyry, diabas or crystallized limestone are especially suitable. Caution is necessary with sandstones, as only siliceous sandstone is durable. The choice of colors of the stone is also relevant. Granite of a uniform grey color and sawn surface can look as dull as simple plain concrete. A harmonious mixture of different colors and slightly embossed surfaces can look very lively, even when the masonry areas are extensive. Surfaces can also be enlivened by bright or dark joint-filling. The sizes of the stone blocks and the roughness of their surfaces must be harmonized with the size of the structure, the abutments, the piers etc. Coarse embossing does not suit a small pier only 1 m thick and 5 m high, but large sized ashlars masonry is suitable for large arch bridges such as the Saalebrucke Jena or the Lahntalbrucke Limburg. Granite masonry was preferred for piers of bridges across the River Rhine, because it resists erosion by sandy water much better than the hardest concrete.
2. Iron:
3. Reinforced and Pre-stressed Concrete:
Concrete is a construction material used in almost all construction works. Having a dull grey color, usually concrete is not preferred in construction like bridges but some of concrete bridges have turned out to be beauties, if someone knows the art. Good concrete attains high compressive strength and resistance against most natural attacks though not against de-icing saltwater, or CO2 and SO2 in polluted air. However, its tensile strength is low, so is not preferred in areas of tensile stresses. For tensile reinforcement of concrete steel bars are embedded into it. Steel bars start functioning when concrete cracks i.e. when concrete can no longer resist further tensile stresses. The cracks remain harmless called “hair cracks", if bars are designed and place correctly. A second method of resisting tensile forces in concrete structures is by pre-stressing.
4. Steel:
Amongst bridge materials steel has the highest and most favorable strength qualities, and it is therefore suitable for the most daring bridges with the longest spans. Normal building steel has compressive and tensile strengths of 370 N/mm2, about ten times the compressive strength of a medium concrete and a hundred times its tensile strength. A special merit of steel is its ductility due to which it deforms considerably before it breaks, because it begins to yield above a certain stress level. This yield strength is used as the first term in standard quality terms.
For bridges high strength steel is often preferred. The higher the strength, the smaller the proportional difference between the yield strength and the tensile strength, and this means that high strength steels are not as ductile as those with normal strength. Nor does fatigue strength rise in proportion to the tensile strength. It is therefore necessary to have a profound knowledge of the behavior of these special steels before using them. For building purposes, steel is fabricated in the form of plates (6 to 80mm thick) by means of rolling when red hot. For bearings and some other items, cast steel is used. For members under tension only, like ropes or cables, there are special steels, processed in different ways which allow us to build bold suspension or cable-stayed bridges.
The high strengths of steel allow small cross-sections of beams or girders and therefore a low dead load of the structure. It was thus possible to develop the light-weight "orthotropic plate" steel decks for roadways, which have now become common with an asphalt wearing course, 60 to 80 mm thick.
The pioneers of this orthotropic plate construction called it by the less mysterious and less scientific name "stiffened steel slabs". Plain steel plate, stiffened by cells or rlbs, forms the chord of both the transverse cross girders and the longitudinal main-girders. Simultaneously it acts as a wind girder. This bridge deck owes its successful application mainly to mechanized welding, which is now in general use and which has greatly influenced the design of steel bridges.
So plate girder construction now prevails, in which large thin steel plates must be stiffened against buckling. Previously, vertical stiffeners were placed by preference on the outer faces; longitudinal stiffeners were then arranged on the inside.
Today all stiffeners are placed on this inside so as to achieve a smooth outer surface allowing no accumulation of dust or dirt deposits that retain humidity and promote corrosion - the "Achilles heel" of steel structures. Modern steel girder bridges now hardly differ from pre-stressed concrete bridges in their external appearance - except perhaps in their color. This is perhaps regrettable, because stiffeners on the outside enliven the plate-faces, give scale and make the girder look less heavy. In addition to plate girders, trusses also take full advantage of the material properties of steel. Very delicate looking bridges can be built by joining slender steel sections together to form a truss. Again welding has improved the potential for good form, because hollow sections can be fabricated and joined without the use of big gusset plates. In this way smooth looking trusses arise without the "unrest" which occurs by joining two or four profiles of rolled section with lattice or plates. Steel must be protected against corrosion and this is usually done by applying a protective paint to the bare steel surface. Painting of normal steels is technically necessary and can be used for color design of the bridge.
The choice of colors is an important feature for achieving good appearance. There are steels which do not corrode in a normal environment (the stainless steels V2A and V4A to DIN 17440), but are so expensive that they are used only for components that are either particularly susceptible to the attacks of corrosion or that are very inaccessible.
From the USA came Tentor steel, alloyed with copper, its 'first corrosion layer being said to protect it against further corrosion. This protective rust has a warm sepia-toned color which looks fine in open country. This type of protection, however, does not last in polluted air and the corrosion continues. For steel bridges, good use should be made of the technical necessity of protecting the steel with paint to improve appearance and to achieve harmonious integration of the structure within the landscape.
Aluminum was occasionally used for bridges and the same form was used as for steel girders. Aluminum profiles are fabricated by the extrusion process which allows many varied hollow shapes to be formed, so that aluminum structures can be more elegant than those of steel. Aluminum profiles are popular for bridge parapets because they need no protective paint.