Activated Sludge Process Design
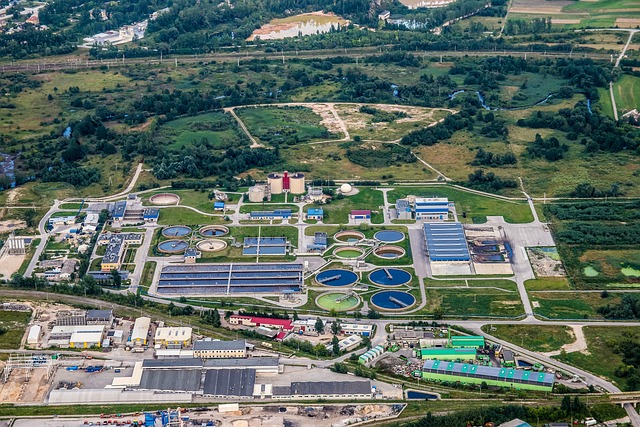
Design of Activated Sludge Systems:
The design of activated sludge systems involves several steps to ensure an efficient and effective wastewater treatment process. Here are the general steps involved:
1. Define the objectives:
Clearly define the objectives of the activated sludge system, such as the desired effluent quality, treatment capacity, and any specific regulatory requirements that need to be met.
2. Characterize the wastewater:
Gather data on the influent wastewater characteristics, including flow rate, organic and nutrient content, temperature, and any toxic or inhibitory substances present. This information is crucial for designing an appropriate treatment process.
3. Determine the design parameters:
Based on the wastewater characterization and treatment objectives, determine the design parameters such as the hydraulic retention time (HRT), solids retention time (SRT), mixed liquor suspended solids (MLSS) concentration, and the desired nutrient removal efficiency (if applicable).
4. Sizing the aeration tank:
Calculate the required volume of the aeration tank based on the HRT and flow rate. The aeration tank provides the necessary environment for microbial growth and organic matter degradation.
5. Determine the oxygen requirements:
Estimate the oxygen requirements for the treatment process, which depend on the influent characteristics and the desired level of organic matter removal. This calculation helps determine the size and capacity of the aeration system, including the diffusers or mechanical aerators.
6. Settling tank design:
Design the secondary clarifiers (settling tanks) to separate the biomass (activated sludge) from the treated effluent. Determine the settling velocity and overflow rate requirements to ensure effective solids separation and a clear effluent.
7. Return sludge and wasting:
Determine the appropriate rate of return sludge (recycle of activated sludge) to maintain the desired MLSS concentration and control the SRT. Additionally, calculate the rate of sludge wasting or excess sludge removal to maintain a balance between the sludge production and the system's capacity.
8. Nutrient removal (if applicable):
If nutrient removal, such as nitrogen and phosphorus, is required, design and incorporate the necessary processes, such as anoxic and aerobic zones, denitrification, and phosphorus precipitation.
9. Provide ancillary equipment:
Design and incorporate essential components, such as screens, grit chambers, and equalization tanks, to remove large debris, grit, and flow fluctuations, respectively.
10. Operational considerations:
Consider operational aspects, such as process control strategies, monitoring parameters, and maintenance requirements. Develop protocols for process control, monitoring, and troubleshooting.
11. Cost estimation:
Estimate the capital and operational costs associated with the design, construction, and maintenance of the activated sludge system. Consider the cost of equipment, energy consumption, chemicals, and labor.
12. Detailed engineering design:
Develop detailed engineering plans and specifications for the construction and implementation of the activated sludge system.
It is important to note that the design of activated sludge systems can vary depending on the specific wastewater characteristics, treatment objectives, and regulatory requirements. Therefore, seeking the assistance of wastewater treatment professionals and consulting design guidelines and standards is recommended for a comprehensive and accurate design.
Design of activated-sludge process involves details of sizing and operation of the following main elements.
- Aeration tank (reactor)-capacity and dimensions.
- Aeration system-oxygen requirements and oxygen transfer system.
- Final sedimentation tank – (deifier)
- Return activated sludge system.SV1
- Excess activated sludge withdrawal system and subsequent treatment and disposal of waste sludge. Since the whole process takes place in a liquid medium the hydraulic regime essentially in the aeration tank and final sedimentation tank.
- MLSS – a mixture of settled sewage + activated sludge dissolved oxygen < 2mg/l
Design Criteria
- F/M ratio = 0.2 – 0.5 day -1 or 0.2 – 0.5 kg BOD's / kg MLSS – d
- Detention time (aeration time) of sewage = 6 to 6 hours
- MLVSS or MLSS = 1500 -3000 mg/l
- Air supply = 10m3/m3 sewage treated
- return sludge = 0.25 -10 of Q (influent sewage flow) Qr / Q = 0.20-0.30 = Vs/100Vs (Volume of sludge)
- Depth = 3-5m
- L=W ratio =5:1
- SVI 50-150 ml/gm