How to Manufacture Lime
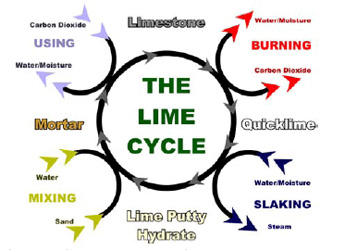
Lime stones are burnt in either clamps or kilns.
1. Clamps:
For small quantity of limestone, burning is done in a clamp. On a clear surface about 5 meters in diameter, layers of broken limestones and fuel are laid to form a heap about 4 meters high. First and the last layers should be of the fuel. In case coal is used as fuel, it could be well mixed up with limestones and lay in a heap. Sides of the heap, which incline slightly inwards, are plastered over with mud to stop loss of heat. A little opening at the top is provided for draught. The clamp is then fired at the bottom.
Disappearance of blue flame at the top is an indication of the burning of lime having completed. The clamp is then allowed to cool down and pieces of quick lime are then handpicked.
Clamp burning of lime is uneconomical as the fuel consumption is more due to loss of heat and as some lime powder is lost in fuel ash. Also the quick lime carries any admixture of ash.
2. Kiln for large quantity of lime, permanent structures of kilns are constructed.
A. Intermittent kiln:
Whenever the lime is desired intermittently or the supply of stones or fuel is not regular then the intermittent kiln is used. An intermittent kiln in which the fuel is not in contact with the lime is shown in the figure. Big pieces of limestones are used to make a sort of archon with which smaller pieces of limestone are loaded. Fire is lighted below the arch formed with big pieces of limestone. It is only the flame not the fuel that comes in contact with the stones. Burning should be gradual so that the stones forming the arch do not get split. It normally takes two days to burn and one day to cool the charge.
B. Continuous kiln:
Wood or charcoal could be used as a fuel. Limestones or kankars free from earth or impurities are broken into small pieces to about 5cm gauge. Alternate layers of 75 mm stone and 6mm coal dust are fed into the kiln. Top should be covered with mud, leaving a hole of 0.5 meter diameter in the center. Burning proceeds continuously and the kiln is not allowed to cool down. Burnt material is drawn out daily and fresh charge of stone and fuel is added from top. Over burnt pieces are discarded whereas the under burnt ones are reloaded into the kiln. Remaining material is slaked or ground in grinding mill for use.
Making fat lime hydraulic - Converting fat lime to hydraulic lime
1. Mixing intimately fat lime with clay:
In proper proportions to make a composition similar to that of natural hydraulic lime and burning it to moderate heat in a kiln. This is called artificial hydraulic lime.
2. Mixing fat lime:
Mixing fat lime with surkhi (grinding the bricks and bates in a mill)