Methods of Natural Seasoning of Wood
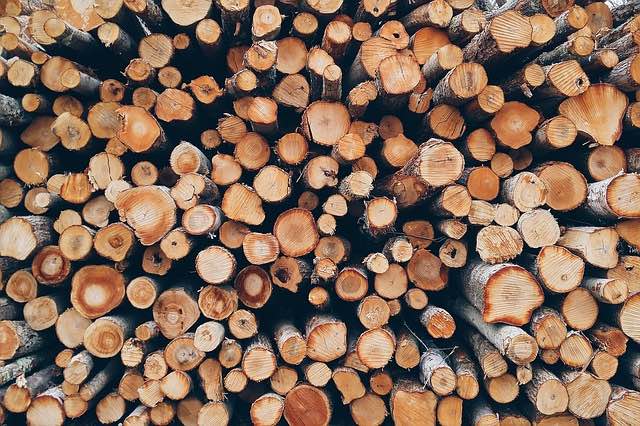
Artificial methods of Seasoning of Wood
Air Seasoning
The traditional method of seasoning timber was to stack it in air and let the heat of the atmosphere and the natural air movement around the stacked timber remove the moisture. The process has undergone a number of refinements over the years that have made it more efficient and reduced the quantity of wood that was damaged by drying too quickly near the ends in air seasoning.
Method of Air Seasoning / Natural Seasoning
The basic principle is to stack the timber so that plenty of air can circulate around each piece. The timber is stacked with wide spaces between each piece horizontally, and with strips of wood between each layer ensuring that there is a vertical separation too. Air can then circulate around and through the stack, to slowly remove moisture. In some cases, weights can be placed on top of the stacks to prevent warping of the timber as it dries.
Moisture loss from the side of the wood is at about the right rate not to cause collapse of the cells, but near the ends of the wood, the moisture loss can prove to be too fast. Often the ends are wrapped or painted to slow the moisture loss from the end grain. While little additional energy needs to be supplied for this type of seasoning, the stacks of timber require a lot of land, represent a potential fire hazard, and the product is not able to be sold for a considerable time. The interest costs on holding stock for long periods can prove significant.
Air-drying of timber is really a more controlled facilitation of what happens to unseasoned sawn, timber, once it is placed into its “work” environment. The amount of drying that can occur is very much governed by the relative humidity of the drying environment and will often vary within individual boards as well as within the stack itself. The time taken for air-drying is a function of the thickness of the timber.
Air-drying is necessarily a slow process, particularly for hardwoods, typically taking 6 to 9 months to reach moisture content in the range 20% to 25%.Air seasoning is the method used with the timber stacked in the open air. It requires the following:
- Stacked stable and safely with horizontal spacing of at least 25 mm.
- Vertical spacing achieved by using timber battens (piling sticks) of the same or neutral species. Today some timber yards are using plastics. The piling sticks should be vertically aligned and spaced close enough to prevent bowing say 600 to 1200 mm max centers.
- Ends of boards sealed by using a suitable sealer or cover to prevent too rapid drying out via the end grain.
- The stack raised well clear of the ground, vegetation, etc to provide good air circulation and free from rising damp, frost, etc.
- Over head cover from effects of direct sunlight and driving weather.
The details depend on the size, quantity and species of the timber. You cannot however expect to obtain less than 16 - 17% mc in the UK. Further seasoning needs to be done inside, in heated and ventilated buildings. Of the methods available for seasoning wood, air drying is the oldest and simplest. Air dried lumber is suitable for exterior use, and green timber is also frequently allowed to partially air dry prior to kiln drying. Since the effectiveness of the drying process depends upon weather conditions which control the drying rate and the final moisture content which can be reached, air drying has been replaced by kiln drying in many areas but is still an important process.
Most air seasoned material is dried in flat piles with stickers placed between layers, but when it is essential to have rapid drying to prevent sap stain, end piling may be used. In humid areas this may be necessary if a dry kiln is not available. Such end racking promotes good air circulation and consequent rapid drying which eliminates the staining problem but often causes end surface checking and warping of the material. Another method of piling once used to promote rapid drying was edge piling.
Although it is generally thought that air drying is a gentle method of seasoning timber, it is often severe depending on the time of the year and the species involved. Material cut from the oaks, sycamore, beech, maple, and other woods which have large rays will surface check readily and consequently thick material cut from these trees is given special treatment. To eliminate rapid end drying, the ends are frequently coated with a material such as paraffin or tar to retard evaporation, but often this is not enough protection, and it is necessary to place the material in what are known as semi-kilns in which the drying rate is still more retarded.
Semi-kilns are often nothing more than covered sheds in which the material is piled, but they may often be large enclosed buildings in which low heat and controlled humidity are used to slow the drying process. In semi-kilns, where the temperature is maintained at 110 °F to 120 °F and fans are used to circulate the air, green stock may be dried to 8 to 12 percent moisture content in 3 months
Piling Lumber for air drying:
The objective of air drying wood is to remove the water in wood by exposing all surfaces of each piece of wood to circulating air. In Missouri, wood can be air dried to a minimum of about 15 percent moisture content, provided the drying time is sufficiently long. It is also necessary to support the wood during drying to prevent the lumber from warping during the drying process. Lumber is piled in a special way to maximize the surface exposure of each piece of lumber to the air and at the same time to support each piece so it will dry straight and without unnecessary warping.
The first consideration is to prepare a strong foundation, 1 to 2 feet above the ground, on which to pile the lumber. The ground beneath the foundation should be kept free of vegetation or debris that would hinder air circulation under the pile.
Your lumber probably will be cut in random lengths and widths. For best results, pile each course so that each board within a layer is well supported and does not protrude at either end of the pile.
This system of piling is called "box piling" and has proven to be the best method of piling random length lumber. The outside boards of each tier are full length. This is important to tie the pile together and make it less subject to tilting or falling over. Leave spaces between adjacent boards approximately equal to the thickness of the boards.
Plan view of a tier of boards, illustrating the system of alternating short lengths for box piling. Unsupported ends of boards placed on the inside of the pile will dry with fewer defects than if allowed to extend over the end of the pile. An adequate supply of wooden sticks (spacers) will be needed to separate each layer (Figures 1 and 2). It is very important that the sticks be uniform in thickness. Sticks usually are cut 3/4-inch thick. Note that the stickers are carefully aligned vertically (Figure 2) so that each layer of lumber will be supported from the base of the pile. If the stickers are not properly aligned, forces will be created in the drying lumber that will result in permanent kinking of the lumber.
Diagram of essential features of good lumber stacking for proper seasoning. Finally, cover the pile with old boards, plywood, corrugated metal or any materials that will protect the top layers of lumber from sun and rain. It is also a good idea to weight the top by placing heavy objects such as concrete blocks or stones on the roof. This will reduce warping in the top tiers of the pile as well as secure the roof on the pile.
Drying time:
In warm weather (April through October), 1-inch lumber can be dried to 15 or 20 percent moisture content in 45 to 60 days (2-inch lumber in 60 to 90 days). In the winter months, lumber will require twice as long to dry. Lumber at 15 percent to 20 percent moisture content is adequate for building unheated structures such as garages or barns. If the wood is to be used inside a heated structure, further drying in a commercial kiln is necessary (6 percent to 8 percent moisture content for indoor use.)